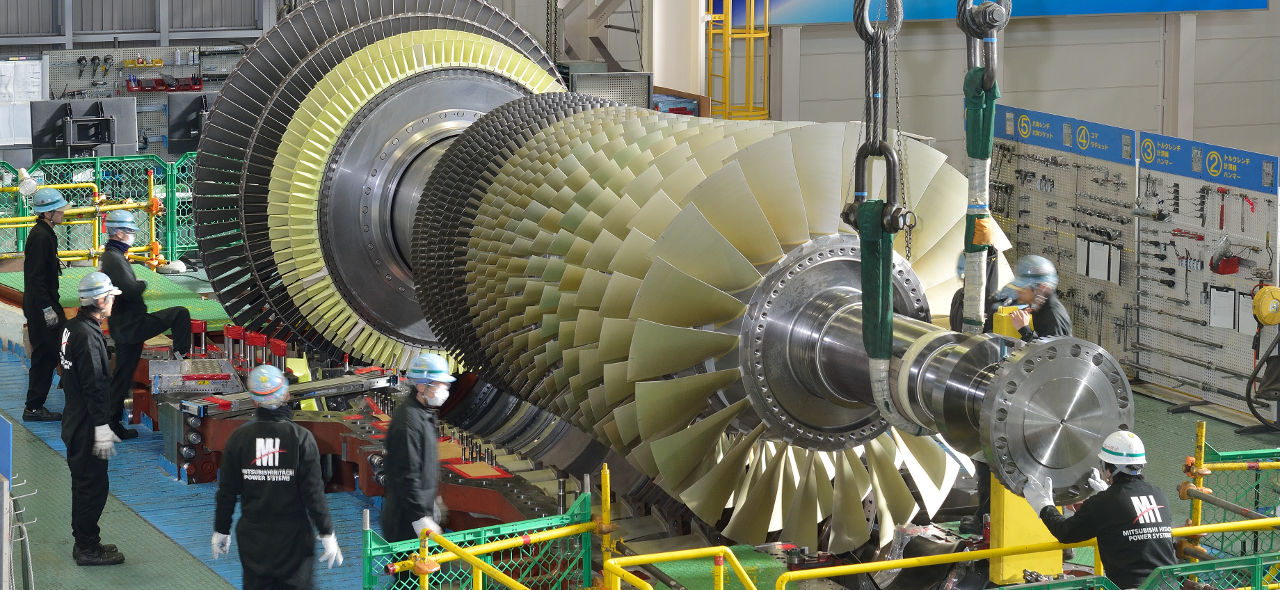
2018.3.29
世界最高水準のガスタービン製造工場に潜入!
2年間の試験!徹底したものづくりを行う「三菱日立パワーシステムズ高砂工場」
日本の電力を支える火力発電所において絶対に欠かせないもの、それがガスタービンだ。一般的に目にすることはほぼないが、実は国を挙げてその高性能化に注力していることをご存じだろうか。研究開発から製造までをワンストップで造り上げ、世界をリードする三菱日立パワーシステムズ高砂工場に訪れた。
エネルギー革新技術の重要拠点
今回、取材班が降り立ったのは、兵庫県高砂市にある山陽電鉄本線荒井駅。多くの有名企業が製品開発の拠点を置く、瀬戸内海に面した工業地域だ。
駅こそ無人駅で寂しい表情を浮かべているが、周囲には巨大な工場や倉庫が立ち並び、方々には周辺企業の施設に、同社の社員寮や社宅。駅前からは、太い道路が南北へとのびている。
幅広の道路を5分ほど南下すると見えてきたのが、火力発電事業で世界第3位の売上実績を誇る三菱日立パワーシステムズ(MHPS)の高砂工場。茨城県日立市や長崎県長崎市など国内5カ所、国外4カ所の拠点工場を持つ中で、液化天然ガス(LNG)によるコンバインドサイクル発電用ガスタービン製造の主力として稼働している。
コンバインドサイクル発電という聞き慣れない言葉。これは、燃料を燃やして発生させた高温ガスの圧力でガスタービンを回し、さらにその排ガスで別の蒸気タービンを回すという二重発電方式のことである。
蒸気タービンのみの火力発電と比べて、同量の燃料でより多くの電力が発電できる上、同じ発電量で排出される二酸化炭素(CO2)量が少ないというメリットがあり、また、LNGを用いることで起動時間が短く、安定した発電が行えるため、季節や時間などによる電力の需要変動への応答性が他の発電方式よりも優れているという。
ちなみに、この技術は経済産業省が低炭素社会実現を担う21の技術を選定した「Cool Earth(クールアース) -エネルギー革新技術計画」(2008年3月5日発表)で、重点的に取り組むべき革新技術の筆頭に挙げられている。
高性能化は現在も国家プロジェクトの一つとして推進されており、MHPSは1700℃級と呼ばれる熱効率の高い新たなガスタービンの技術開発を担っているのだ。
-
コンバインドサイクル発電のしくみ
超巨大ガスタービン製造の最前線
「まずはガスタービンというものが、どのような部品から構成されていて、どんなふうに製造されているのかということを知ってもらうために、組立専用工場に行きましょう」
施設内を案内してくれた三菱日立パワーシステムズ ガスタービン技術総括部長の正田(まさだ)淳一郎さん。同社のガスタービン事業をけん引する一人であり、ジェットエンジンなどの部品を個人的に収集する生粋のタービンマニアでもある。
正田さんに付いて施設内に入ると……
とにかく広く、天井が高い。
この組立専用工場では、高砂工場内で製造されたガスタービンのパーツを組み立て、製品として出荷するまでの工程を担っている。多種多様な工作機器が並ぶような一般的に思い浮かべる工場とは違い、とにかくスッキリとした印象だ。
とはいえ、そこかしこに並べられた巨大な部品。外装用など一部を除き、全てのパーツを高砂工場内の各所で製造しているそう。これらを組み合わせてできるのが……
ほぼ完成形というガスタービン。外装などを含めて、ここまで組み立てるのに、専門職5~6人体制でおよそ1カ月かかるという。この中に組み込まれているのが…
ガスタービンの本体。横にいる人と比べれば、そのサイズは一目瞭然だろう。全長約16m、総重量約500t。「M701F」と呼ばれる1400℃級のこれ1台で、385MW(38.5万kW)を発電するパワーを持つ。
「ガスタービンは主に圧縮機、燃焼器、タービンで構成されています。圧縮機が空気を吸い込み、圧縮して燃焼器へ送ると、燃焼器が圧縮された空気で燃料を燃やし、1600℃や1650℃といった超高温の高圧ガスを作ります。その圧力によってタービンを駆動させ、発電する仕組みになっています」(正田さん)
先ほどから出てくる1600℃や1650℃という温度は、タービンの入口の温度を指している。入口温度とはつまり、タービンの耐久温度。温度をより高めれば高圧ガスの出力が上がり、タービンを回転させるエネルギーも上がる。すると燃費が良くなり、発電効率、いわゆる熱効率が上がるのだそう。
1700℃級という高性能マシンを実現するためには、圧縮機、燃焼器などの性能向上はもちろんだが、タービンの翼をいかに頑強にできるかがカギ。そのため、耐熱材料の開発、冷却技術、遮熱コーティング技術といった要素技術の研究は重要視されている。
愚直なまでに実証実験に命を懸けるエンジニアたち
続いて正田さんが案内してくれたのは、三菱重工業総合研究所。ここではガスタービンをはじめ、原子力発電プラントやジェット機用エンジン、ロケット用エンジンなどの製造技術開発を担う30の研究棟が集まっている。
まず見せてもらったのは、タービン翼の違いだ。
右から普通鋳造、中央が一方向凝固、左が単結晶という技術で鋳造したタービン翼。これを円形に並べてタービンを形成する。
普通鋳造したタービン翼は、金属の結晶同士が接合して形成されており、接合面の強度が比較的もろいデメリットがある。これを解決したのが一方向凝固という技術。金属を縦方向に引き伸ばすように鋳造していくため、普通鋳造の翼より高強度になったという。
さらに単結晶のタービン翼は、普通鋳造のものにあるまだら模様の一つの結晶だけで翼を丸々形成しており、金属の接合面がないためどの鋳造方法よりも耐久性に優れたもの。しかし、製造すると金よりも高価になるため、実用化はまだまだ先だという。
その巨大さに目が行きがちだが、ガスタービン製造においての最重要技術がこの「鋳造」にある。金属を溶かして鋳型に流し入れ器物を造るという昔ながらの技術をこの規模で手掛けられる企業は、同社を含め世界に3社しかないそうだ。
続いては、1600℃級ガスタービンの実用化に大きく貢献したフィルム冷却技術。空気が通る穴を開け、タービン翼自体の温度を下げる。穴の形状は翼を冷やすための表面積を広げるため、円ではなくアヒルの足のような形をしている。
翼の部位によっては空気の流れが変わってしまうため、穴は整然と並べられているわけではなく、角度も形状もわずかに変えて形成されている。
また、フィルム冷却の性能をさらに向上させるためには、ますます穴の形状が複雑化していくるという。そのため近年では3Dプリンターでの開発実験も行っているそうだ。
その他にも、検証実験は多数。
大型の低速回転試験装置を使い、フィルム冷却技術による空気の流れなどを検証する空力実験場(写真上)や、燃焼器の故障の原因となる振動現象を抑えるための燃焼振動実験(写真下)を見せてもらった。
「燃焼振動や動翼回転時の気流は、シミュレーションしたとしても実証実験をすると予測できない結果が必ず出てしまうんです。そのため担当する研究者たちは、愚直に実験を繰り返し、何度も点検して、万全の状態を目指しています」(正田さん)
世界で唯一無二!性能を見極めるT地点
研究室から生まれた技術は、実際に部品として製造され、ガスタービンとして組み立てられる。だが、製品として世に出るのはまだ先だ。最後に訪れた実験設備で試験運転をクリアしてからになる。
敷地の東南に位置するガスタービン複合サイクル発電プラント実証設備。通称「T地点」と呼ばれ、自動車の走行テストのように、プロトタイプの長期的な実験運転を行っている。
まさに今、試運転中のガスタービンがあるそうなので、実際に見せてもらうことに。建屋に入り、扉を開けると……
とにかくすさまじい大音響。
空気の圧縮音やマッハ1で回るタービンの回転音、燃料が燃え盛る音が混じり合い、隣に立つ正田さんの声も、全く聞き取れない。
室内の広さの問題もあり、ガスタービンの全貌を見ることができなかったが、しかし少し想定していたイメージと違った。組立現場で見たむき出しの鉄感がない。
それもそのはずなのだ。タービン内はおよそ1500℃の高温。断熱材で周囲を保護していなければ、そばに立つことなど不可能である。
建屋の外へ出ると、ガスタービンからつながる排熱回収蒸気発生器が高くそびえていた。ガスタービンからの排ガスがここに送られ、蒸気を作り、別のタービンを回す。まさにコンバインドサイクル発電システムを擁した火力発電所そのものなのだ。
試験は2年間かけて行われる。半年ごとに一度運転を停止して、状態を確認するという。製品を販売する前の検査は当然だろうと思うかもしれないが、実は海外企業は、この試験運転を実施していない。
製造は販売に直結し、故障したら対応するという考え方が一般的で、需要も限られている上、莫大なコストがかかるため、いちいちプロトタイプを造って実証実験を行っていては採算が合わないことが原因だ。
その中で、MHPSだけが実証実験設備を保有している。つまり世界で唯一の施設なのだ。
事実、世界各地で26台商用運転中というMHPS製の1600℃級ガスタービンは、そのうちの21台が8000時間以上稼働し、事故停止率が0.5%と驚異的な数値をたたき出している。長期稼働への信頼性を高める実験が功を奏していることは、うなずけるだろう。
ちなみに正田さんによると、T地点のガスタービン単体で、姫路市の世帯数の電力に相当するポテンシャルがあるそうで、しかも試運転で発電された電力は、電力会社に供給しているのだとか。実に合理的だ。
MHPSは現在、1700℃級ガスタービンを実現する過程で実用化のめどがついた技術を活用し、次世代機である1650℃級ガスタービンを開発中。2019年に着工し、2023年稼働を目指している。それと同時に現在のT地点を廃止し、2020年の稼働に向けて新たな実験設備の建設も始めている。
納得する成果が得られるまで商品を売らない姿勢を貫くMHPSのエンジニアたちのプライドは、着実に自らを鍛え続け、MHPS製ガスタービンを世界トップレベルに押し上げた。さらに価値を高めようとたゆまず邁進し続ける姿には恐れ入る限りである。1700℃級ガスタービンの革新的技術の開発、実用化ももはや時間の問題だ。
-
この記事が気に入ったら
いいね!しよう -
Twitterでフォローしよう
Follow @emira_edit
text:伊佐治 龍