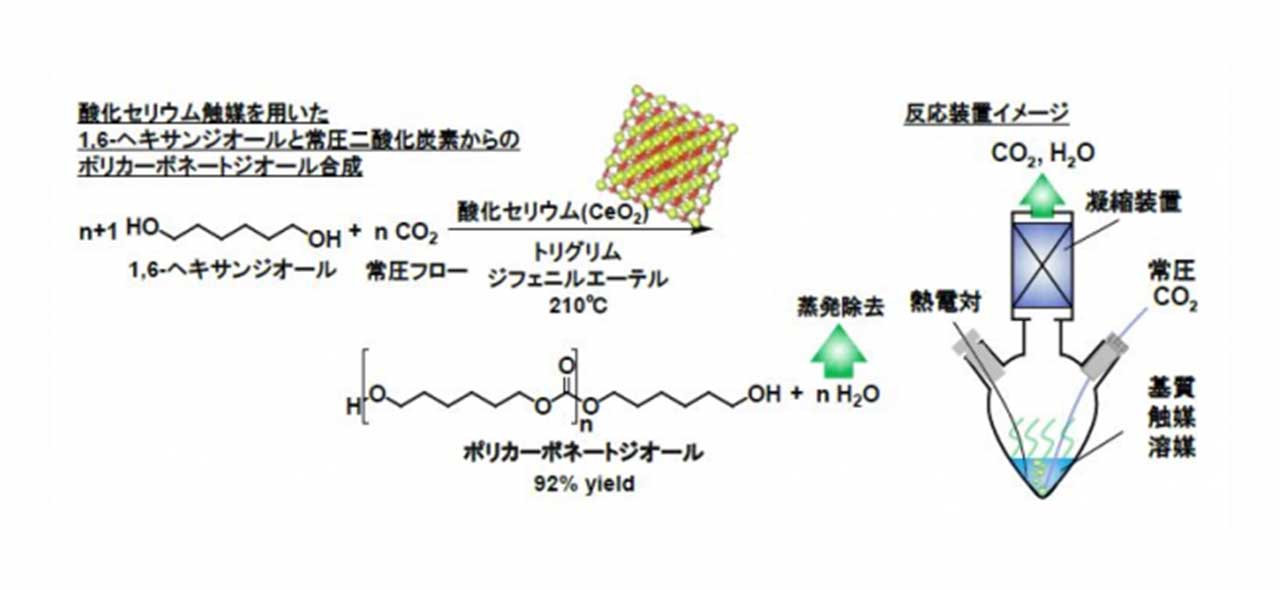
2022.01.06
CO2からプラスチックを合成! 日本製鉄らが挑む世界初の触媒プロセスが脱炭素社会にもたらす効果
有毒な原料から二酸化炭素(CO2)に代替し、ウレタンの原料であるポリカーボネートジオールを生成
2021年7月、日本製鉄株式会社と大阪市立大学、東北大学で構成される研究グループは、常圧の二酸化炭素(CO2)を利用し、プラスチックを直接合成する触媒プロセスの開発に成功した。これはカーボンリサイクルを推し進めると同時に、従来のプラスチック合成プロセスにおける問題も解消できる画期的な成果でもある。その問題とは何なのか?そして今後のプラスチック合成にどのような変化をもたらすのか──。日本製鉄株式会社先端技術研究所 中尾憲治課長に、今回のカーボンリサイクル研究の経緯、今後の可能性について解説してもらった。
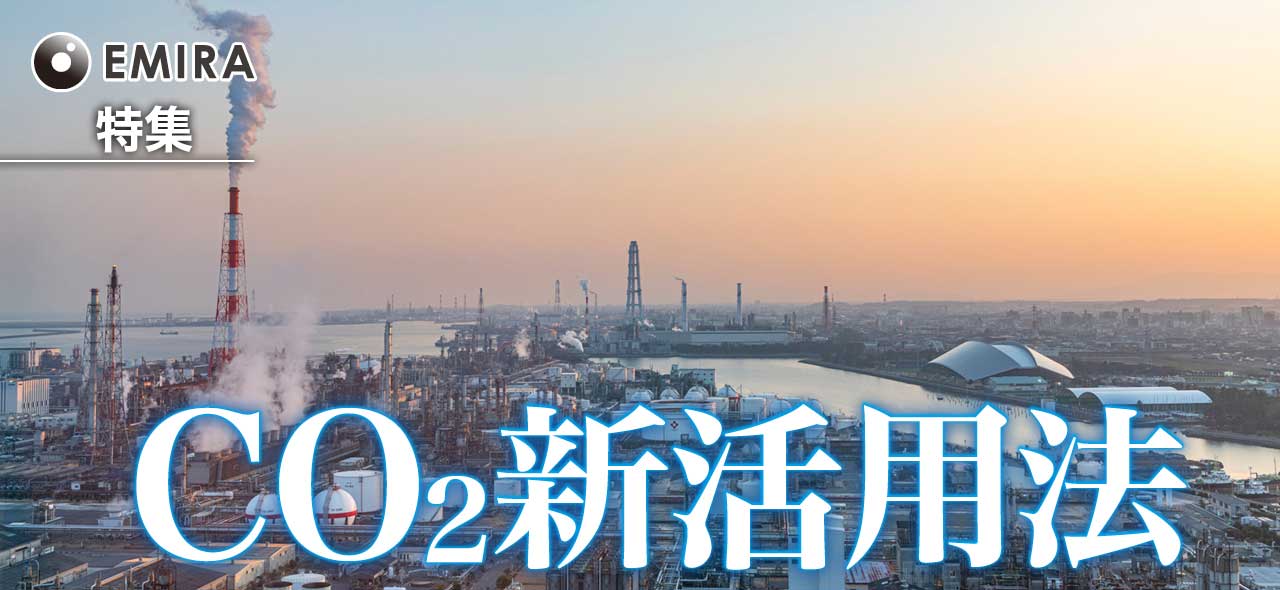
- 第1回
- 第2回CO2からプラスチックを合成! 日本製鉄らが挑む世界初の触媒プロセスが脱炭素社会にもたらす効果
- 第3回
- 「CO2の新活用法」に戻る
既存合成の“グリーンケミストリー”化を目指して
今回の研究は、常圧のCO2とジオール(2つの水素基が2個の異なる炭素に結合した化合物の総称)から、プラスチックに代表されるポリウレタン合成の重要中間体であるポリカーボネートジオールの直接合成を行う触媒プロセス。
従来の合成と異なり、脱水剤を用いる必要もなくなった。
-
ポリカーボネートジオールの合成イメージ。ポリカーボネートジオールは、プラスチックに代表されるポリウレタン合成の重要中間体である
画像提供:日本製鉄株式会社
「通常、ポリカーボネートジオールの合成には、ホスゲン(塩化カルボニル)や一酸化炭素(CO)が原料に用いられてきましたが、これらの原料は有毒であるため、グリーンケミストリーの観点から代替する原料を用いた合成手法の開発が求められていました」
そう話す日本製鉄株式会社先端技術研究所の中尾憲治課長は、2006年ごろから東北大学大学院工学研究科応用化学専攻の冨重圭一教授と共に、CO2の有価化に関する共同研究を行い、CO2を原料に化学品を製造する触媒プロセスの研究を重ね、2018年から大阪市立大学人工光合成研究センターの田村正純准教授と共に、ポリカーボネートジオール合成の研究を開始した。
-
「CO2からポリカーボネートジオールを合成できれば、環境負荷の高い猛毒物質を用いず、安価で安全なグリーンなプロセスにできるのではないかという発想が、研究の始まりでした」(中尾氏)
CO2を代替原料に用い、ジオールと反応させてポリカーボネートジオールを合成する、この方法は、水のみを副生する。
「CO2を原料に用いるためにその反応性を向上させるには、温度を上げたり圧力をかけたりする必要があります。冨重先生との研究では、まず5MPa(メガパスカル、50気圧)という高圧をかけて反応させ、さらに副生される水をいかに除去させ、反応の進行を早めるかという課題に取り組みました」
-
脱水剤を用いず低圧で反応が進めばプロセス全体の省エネ化につながると考え、2018年より国立研究開発法人新エネルギー・産業技術総合開発機構(NEDO)の委託事業(先導研究プログラム/未踏チャレンジ2050)となる
画像提供:日本製鉄株式会社
今回の研究・開発において、日本製鉄は触媒のプロセスや全体のフロー検討を、グループ会社の日鉄エンジニアリング株式会社と共に担っている。
「具体的な例としては、製鉄所から発生するCO2の分離回収からがプロセスとなるのですが、CO2は日鉄エンジニアリングの分離技術で回収することを想定しています。このCO2をどのように反映させるかを当社グループで考え、反応を加速させる触媒は何か?どんな反応形式で進めるべきか?という実験の検討を大阪市立大学と行ってきました」
プロセス検討、反応条件検討を重ね今回の研究成果に至るが、これからはラボスケールでの検討からスケールアップさせ、規模とマテリアルフローを見ながら実用化に向けた反応器やプロセスを検討。そのためにエンジニアリングデータを取る必要があるという。
無用だったCO2を資源に、無毒な合成を実現
今回の研究で特に注目したいのが、CO2を代替原料とすることで、CO、ホスゲンなどの猛毒物質の使用が抑えられる点だ。
「従来、COやホスゲンを用いてジメチルカーボネートが作られます。これとジオールを反応させてポリカーボネートジオールを合成、ポリウレタン製品が作られてきました。このプロセスがCO2とジオールを直接合成することでそっくりそのまま置き換えられるわけです」
プロセス移行実現への鍵となるのが、触媒に酸化セリウムを選択することと、副生水の除去方法だった。
「脱水剤を用いず水を除去するために着目したのが、生成物やジオール、水の“沸点差”でした。常圧のCO2を吹き込むことで水を蒸留除去し、ポリカーボネートジオール合成が進行すると考え、実証の結果、水だけを選択的に飛ばすこと、蒸留しながら反応させることでポリカーボネートジオールを高選択率かつ高吸収率で得ることに成功しました」
-
副生水の除去方法に関する検討図。従来の汎用法では脱水剤を用い分離していたが、装置内でCO2を流通させ、副生水を蒸留させる方法により反応を加速させることにつながった
画像提供:日本製鉄株式会社
また今回、CO2を常圧で用いたのには、「ラボスケールの実験器具では、常圧でしか実験ができなかったというのが、正しい表現です」と説明を置いた上で、中尾氏は「CO2の反応を促進する点では、多少圧力をかけた方がいいという結論に至っており、今後は、圧力をかけることで、さらに反応性を向上させていくつもりです。CO2の導入方法もエンジニアリングの観点での検討がこれから必要になるでしょう」
この成果を実用化させる上で、最も重要な課題は、合成に要する「時間の短縮化」だという。
「このプロセスでのポリカーボネートジオールの合成には、現段階で72時間以上要し、96時間ほどを要すると生成物収率が92%に上昇することが分かっています。実用化には、この時間を半分から3分の1ほどに短縮させ、同等の反応性が得られるようにする必要があると考えています」
実用化までを10段階で例えると、「現在は3段階あたり」と中尾氏は考える。
「この後ベンチ試験で実証できれば5、6段階へ、その後パイロットまで行けば8、9段階までたどり着き実用化が見えてくるはずです。国のロードマップにも記されているように、2030年代の実用化に向け、事業者や化学メーカーと一緒に取り組んでいきたいと考えています。
コスト面などの課題は、CO2導入の最適量や反応条件の最適化などマテリアルバランスやエネルギーバランスを実験データで蓄積し、プロセス全体のフローが確立した後、経済性の評価・検討ができると考えています。これが来年度中の目標です」
製鉄、製プラを持続させながら目指すカーボンニュートラル
CO2を用いた、この画期的なプラスチックの直接合成について、日本製鉄では、今後どのような応用、または可能性を考えているのだろうか。
「今回の成果は、ポリカーボネートジオール以外のポリエステル系ジオールの合成にも対応可能だと考えています。応用が実現すれば市場拡大にもつながりますし、そこに含まれるCO2固定量も自然と増えていきます。沸点の差がポイントになる合成ですので、もちろん応用可能な原料には限りもありますが、水の沸点である100度より高沸点の物質が使えれば、いろいろな製品を作り分けることが可能でしょう」
脱炭素社会の実現に向けて、日本製鉄では2021年3月に「日本製鉄カーボンニュートラルビジョン2050~ゼロカーボン・スチールへの挑戦~」を策定。
今回の研究を含めてカーボンリサイクル、そして“ゼロカーボン・スチール”の実現に挑戦している。
「鉄鉱石や石炭を使い高炉や電炉で鉄を作る従来のプロセスは、多量のCO2を排出してしまうため、日本製鉄では現在、『ゼロカーボン・スチール生産プロセス』を考えています。高炉や電炉を用いつつ、カーボンフリーな水素を原料とする直接還元プロセスの開発にも取り組んでいます。また、電炉の大型化による高級鋼の製造、さらには水素還元製鉄にチャレンジし、カーボンオフセット対策なども含めた複線的なアプローチでカーボンニュートラルに取り組んでいます」
-
日本製鉄が考える高炉・電炉におけるCO2排出削減施策のロードマップ。2030年までにCO2排出量の2013年比30%削減や高炉水素還元プロセスの開発を進めている
画像提供:日本製鉄株式会社
脱炭素という言葉も着々と浸透してきた中、日本製鉄は「化学メーカーをはじめとする事業者と連携した事業の実現を目指しています」とも、中尾氏は話す。
ポリカーボネート、ポリエチレンテレフタレート(PET)などのエンジニアリングプラスチックに対し、CO2を原料に製造する技術を確立し、技術が一般化すれば、プラスチックを作りながら温暖化を防ぐ新潮流が生まれ、プラスチック問題にも一石を投じるのではないだろうか。
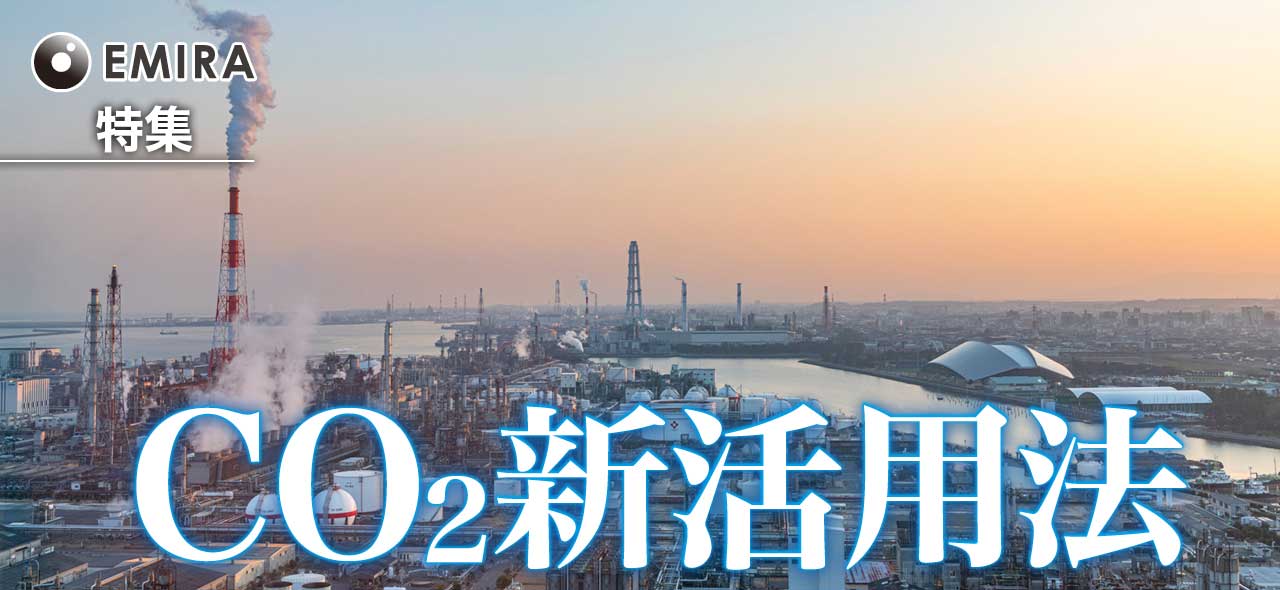
- 第1回
- 第2回CO2からプラスチックを合成! 日本製鉄らが挑む世界初の触媒プロセスが脱炭素社会にもたらす効果
- 第3回
- 「CO2の新活用法」に戻る
-
この記事が気に入ったら
いいね!しよう -
Twitterでフォローしよう
Follow @emira_edit