- TOP
- 特集
- 市場規模拡大が予想される「CFRP」
- 炭素繊維とは? 新素材CFRPの将来性と今後の課題
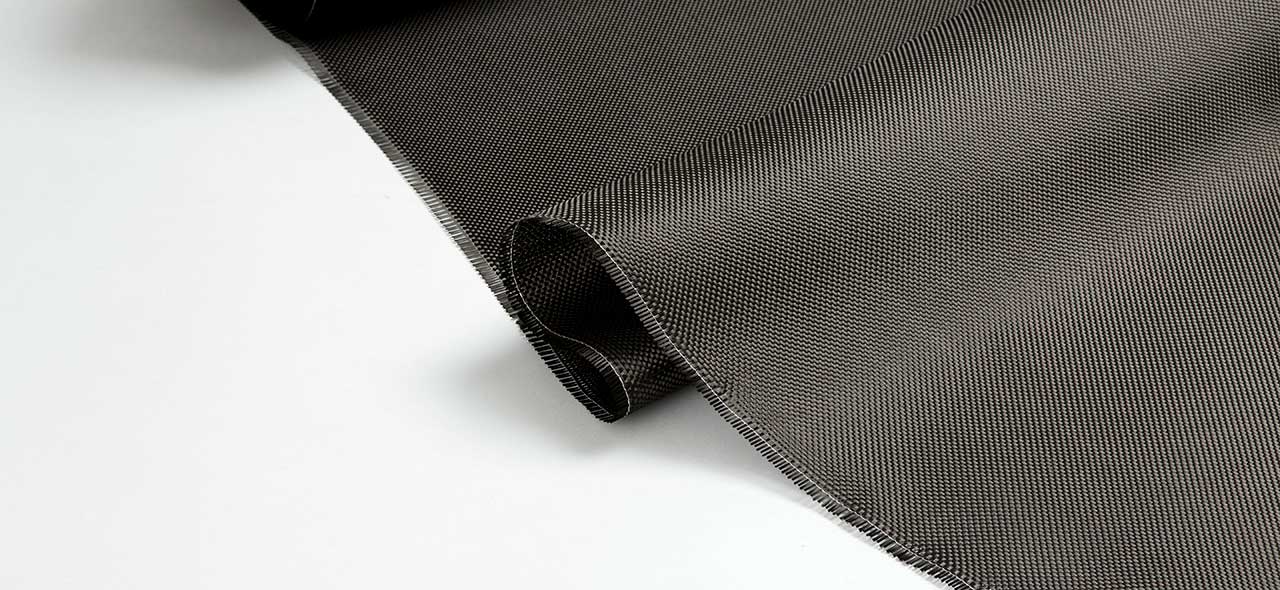
2022.04.19
炭素繊維とは? 新素材CFRPの将来性と今後の課題
鉄やコンクリートよりも軽くて強靭(きょうじん)な素材
「炭素」はダイヤモンドから黒鉛まで、実に多様で幅広い物質を構成し得る元素である。その炭素が持つ強靭さを繊維として利用したのが炭素繊維、いわゆるカーボンファイバーだ。炭素繊維は今、航空宇宙分野、産業分野、スポーツ用品に至るまでさまざまな領域で需要が急速に拡大している。なぜ今、炭素繊維が注目されているのか? そもそも炭素繊維にはどのような特性があるのか。炭素繊維研究の第一人者で、現在は金沢工業大学 高信頼理工学研究センター所長を務める影山和郎氏に詳しく説明してもらった。
TOP画像:東レ株式会社
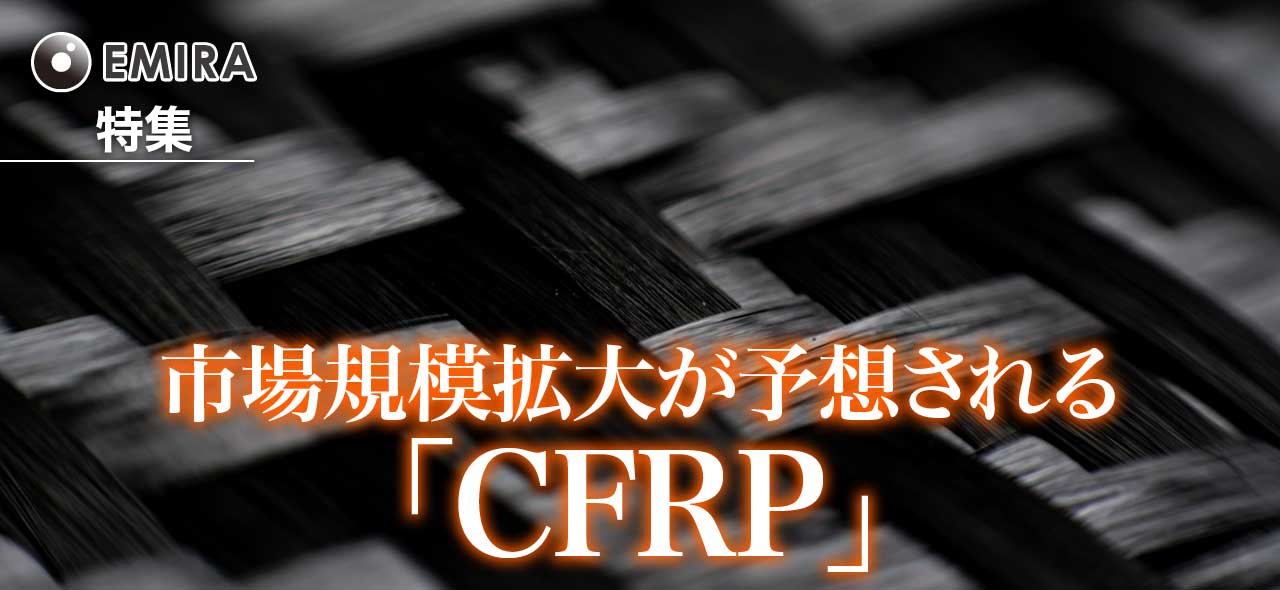
- 第1回炭素繊維とは? 新素材CFRPの将来性と今後の課題
- 第2回
- 第3回
- 「市場規模拡大が予想される「CFRP」」に戻る
軽くて強い、機械的特性に優れた炭素繊維の発見
現代社会において“炭素”と聞けば、「脱炭素」「カーボンニュートラル」というキーワードを連想する人が多いのではないだろうか。
ここで言う炭素やカーボンは地球温暖化の要因とされる二酸化炭素(CO2)のことであり、本来であれば「脱二酸化炭素」「CO2ニュートラル」と呼ぶのが筋かもしれない。
炭素は石油、石炭、木炭など有機化合物に含まれている元素であり、炭素単体(同素体)としてもダイヤモンドから黒鉛まで実にさまざまな物質として存在するのが特徴だ。
有機化合物内の炭素が燃焼などによって酸素と結び付くとCO2となって放出されるが、このとき酸素を遮断して不完全燃焼させると炭素だけを取り出すことができる。代表的な木炭は、生成も容易で紀元前から人間の手で作られてきた。
その炭素を、繊維という形で生成したのが炭素繊維であり、カーボンファイバーだ。
「線状の炭素を作るのはそれほど難しくありません。例えば日本の竹から作ったエジソンの白熱電灯用炭素フィラメントが有名です。しかし、炭素の結晶構造(グラファイト)を制御して欠陥のない均質で高強度の炭素繊維を作ることはたいへん難しい。今から60年ほど前、その炭素繊維に強度を与えたことが革新的でした。炭素繊維を最初に作ったのは米国のユニオンカーバイド社でしたが、それとほぼ時を同じくして、通商産業省(現・経済産業省)工業技術院の進藤昭男博士が『ポリアクリロニトリル』というアクリル繊維を使ったPAN系*炭素繊維の基本技術を発明したのです」と金沢工業大学 高信頼理工学研究センター所長の影山和郎氏は炭素繊維誕生の歴史を説明する。
*アクリル繊維を使った炭素繊維はPAN系とピッチ系に区分される。もう一つのピッチ系は石油・石炭などの副生成物を原料とした物を高温で炭化して作った繊維を指す
-
東京大学を卒業後、1981(昭和56)年に通商産業省工業技術院機械技術研究所に入所。次世代産業基盤技術研究開発制度・複合材料の研究開発に取り組んだのが炭素繊維との出会いで、「私の研究者人生は炭素繊維と共にあった」と語る
炭素繊維用の原料になる繊維(プリカーサ)の直径は1本当たり5~15ミクロンと、髪の毛の10分の1ほどしかない。その細い繊維を耐炎化処理後、加熱炭化処理することで強固な炭素繊維が作られる。炭素同士の結合は非常に強固でありながら密度は低い。つまり、軽くて強いことが最大の特徴だ。
「例えば機械部品によく用いられるステンレス鋼と比べると、引っ張り強度は約10倍です。密度(体積当たりの質量)は4分の1ほどで、比強度(重量当たりの強度)は約40倍という軽量化による省エネルギーに大いに貢献できる機械的特性を持っています。強度だけでなく弾性率も高いという特性は他の材料ではまず到達できません。現在、私たちのまわりにある製品に広く適用されている工業材料の中で、人類が手にした最強の材料と言えるでしょう」
ここで言う強度と弾性率の違いをごく簡単に表すならば、強度とは“壊れにくさ”であり、弾性率とは“変形のしにくさ”だ。
つまり、部材に求められる強靭さの条件が同じならより軽く作れ、同じ重量ならより強靭に作れるのが炭素繊維なのだ。
-
物質の弾性率と強度の関係を解説する影山氏。強度は高いが変形しやすい(=弾性率が低い)物質もあれば、その逆もある。炭素繊維は強度も弾性も金属や他の化学繊維より圧倒的に優れており、しかも軽いのだという
「PAN系炭素繊維の材料となるポリアクリロニトリルは衣料品などにも用いられる一般的な材料ですが、炭素繊維の材料に用いられるのはそれとは異なる特別なポリアクリロニトリルです。この材料を見つけたことで炭素繊維の性能が大幅にアップしました。それが東レ株式会社(※本特集3本目に登場)による炭素繊維の実用化につながったのだと思います」
先述の通り、炭素繊維を最初に作ったのは米国企業だが、それを工業製品に足るレベルにまで高性能化したのは東レをはじめとする日本の合成繊維メーカーだ。
PAN系炭素繊維に続いてピッチ系と呼ばれる炭素繊維も開発された。綿のような短い繊維で構成され、断熱材などに使用される等方性ピッチ系炭素繊維を呉羽化学工業株式会社(現・株式会社クレハ)が開発。人工衛星の構体などにも使われる高弾性率の異方性ピッチ系炭素繊維は三菱樹脂株式会社(現・三菱ケミカル株式会社)、日本グラファイトファイバー株式会社が工業化に成功した。
まさに炭素繊維製造において、日本は世界のリーダーと呼べる存在になった。
-
世界中の市場に供給されるPAN系炭素繊維の約6割は日本のメーカーが生産したもの。世界全体におけるPAN系炭素繊維生産能力15万8000トンのうち、半数以上となる8万3400トンを東レ、帝人株式会社、三菱ケミカルの3社が担っている
画像提供:東レ株式会社
炭素繊維の強靭さを生かして成形できるCFRPに
しかし、炭素繊維の機械的特性がいかに優れていても、繊維の状態では工業製品としての用途に乏しかった。PAN系炭素繊維の基本技術を形作った進藤博士自身も、当初は「プラスチック素材の強化材」という可能性に気付いておらず、研究論文などでは弾性の高さよりもむしろ糸や布として利用できる柔軟性が強調されていたという。
現在、カーボンと聞いてパッと思い浮かぶのは、平織りされた繊維の模様が表面にある黒い塊だろう。
これは炭素繊維を樹脂の強化材として用いたCFRP(Carbon Fiber Reinforced Plastics/炭素繊維強化プラスチック)と呼ばれる複合材料だ。CFRPはエポキシなどの樹脂を母材として炭素繊維を強化材に用いるが、この複合材料としての用途こそ炭素繊維の価値といえる。
「CFRPは母材となる樹脂を何にするか、どんな炭素繊維を選ぶか、炭素繊維をどのような方向で入れるか、どのような製造方法で作るかといった選択肢によって、使用する部位ごとに適性化されたさまざまな特性を付与できます。例えば同じ航空機の中でも、主翼など真っすぐでとにかく強度を高めたい部位には炭素繊維を単一方向に並べたCFRP、曲がりくねった部位にはファブリック材(織物)のCFRP、と使い分けられています」
CFRPは炭素繊維ならではの強靭さを保ったまま、任意の形状に成形が可能だ。
その結果、産業機械から航空機、レーシングヨットなどの船体やスポーツ用品に至るまで、幅広く普及することになる。
CFRPとしての市場は1980年代から徐々に開拓され、1990年代後半から産業用途が急増。特に2010年以降は急速に需要が拡大し、今では1兆2464億円の世界市場規模(2020年時点)にまで拡大した。
今後もさらに市場は拡大し続け、2035年には現在の3倍近くにまで達するという予想もある。
-
大きなものでは長さ100mにもなる風力発電機のブレード。たわみを防ぐために、スパーキャップと呼ばれるCFRP製補強板が不可欠となる
将来的な市場の中で特に期待されているのが、風力発電ブレード用途だ。
「風力発電のブレード本体はガラス繊維複合材料(GFRP)で製造されますが、大型のものだとブレードがたわんでしまい、支柱にぶつかったり破損したりする可能性があります。そこで、たわみを防ぐために、ブレードの中にCFRPのスパーキャップと呼ばれる補強材を入れるのです。今、世界中で風力発電は増えており、今後も洋上風力などでブレードが大型化されるといわれていますから、CFRPの需要はますます高まっていくでしょう」
エネルギー分野の他に、自動車用途も拡大が期待される分野の一つ。
車体の軽量化が航続距離などの性能と直結するEV(電気自動車)などにおいてはさらなる高性能化を実現する材料として普及が目指されるほか、軽量性や高強度が求められるFCV(燃料電池車)用水素タンクなどもCFRP以外に選択肢がない部位の一つだ。
他の材料で代替が効かないところこそ、CFRPの強みに違いない。
奇妙な言い回しだが、これからの脱炭素社会実現に向けて、炭素繊維は欠かせない存在なのである。
需要増が期待される炭素繊維に残された課題とは
期待値の高いCFRPではあるが、大量生産品として採用されるにはまだ多くの課題がある。
一つは炭素繊維を作るのに大量のエネルギーを使うこと。従来の製造方法では繊維の耐炎化・加熱炭化といった複雑かつ高エネルギーな前処理が必須で、結果としてコストが高くなってしまう。それ以外にも、大量に合成することが難しく、供給量を増やせないという問題もある。
「2011年にスタートした『革新炭素繊維基盤技術開発』という経済産業省の国家プロジェクトで、私や東京大学を中心とする産学官連携体制の下、新しい製造方法が開発されました。この手法では従来必要だった耐炎化工程が不要となり、外部からの加熱でなくマイクロ波で炭素化させる最新技術の投入で、製造時のエネルギーを大幅に低減できたのです。原料は同じままで、従来のPAN系炭素繊維と遜色のない弾性と強度を得られることが確認されました」
この「革新炭素繊維基盤技術開発」は、現在もプロジェクト参加企業による実用化に向けた検討が続いている。生産・製造設備の大幅な入れ替えが前提であるものの、技術的に可能であることは既に実証されており、今後の実用化が期待されているところだ。
さらにCFRPを製造する工程においても、従来のオートクレーブ(樹脂を高温高圧にするための専用窯)で硬化させる成形方法に代わり、樹脂を型に注入するRTM(レジントランスファーモールディングの略)成形、熱硬化性樹脂の代わりに熱可塑性樹脂(高温下で軟化し、冷やされると硬化する性質の樹脂)を使用する射出(しゃしゅつ)成形など、多様な成形方法が登場。製造時のエネルギーの低減と時間短縮、コスト削減が実現しつつある。近い将来、市場が拡大すれば大量生産によるコスト減も期待できるだろう。
もう一つの課題はリサイクル性。現在、一般的な金属や樹脂のリサイクルはかなり進んでいるが、炭素繊維については大部分がリサイクルされず、埋め立て処理されている現状だという。
「これは炭素繊維と樹脂が混ざり合っているCFRPの構造的な問題です。炭素繊維を取り出すには樹脂を全て取り除かなければいけませんので、熱分解する方法や化学的に熔解する方法などさまざまな手段が検討されています。技術的にはできても、リサイクルするために大きなエネルギーを消費するのでは本末転倒です。現在はリサイクル性を高めるために、その適切なバランスを探っているところになります」
-
炭素繊維やCFRPの新たな製造方法の開発だけでなく、アメリカズカップのレーシングヨット開発など幅広い分野における炭素繊維の活用方法を模索してきた
今後、炭素繊維のリサイクルが進めば、再利用品を活用した新たな市場も形成されるに違いない。ただ、影山氏には、リサイクルとは違う方法で環境に貢献するアイデアがあるそうだ。
「リサイクルが難しいなら、極めて長い期間にわたって使えるものを作ればいいのです。例えば、ビルや橋などの構造体ですね。CFRPという材料は単に強靭なだけでなく、化学的に極めて安定しており長期耐久性も極めて高い。100年くらいであれば軽く持ちますし、鉄やコンクリートなどが朽ち果てても炭素繊維は最後まで残りますから」
それでも100年後には寿命が訪れるわけだが、その頃には当然リサイクル技術も進み、逆に再利用できる炭素資源としてその希少価値にスポットが当たっている可能性もある。その時点でまだ環境破壊や資源枯渇が問題になっているようなら、それこそ大問題だろう。
炭素繊維の優れた特性とどう向き合い、どのように生かしていくのか──。
その答えが見つかった時に、大きなイノベーションが起こるかもしれない。
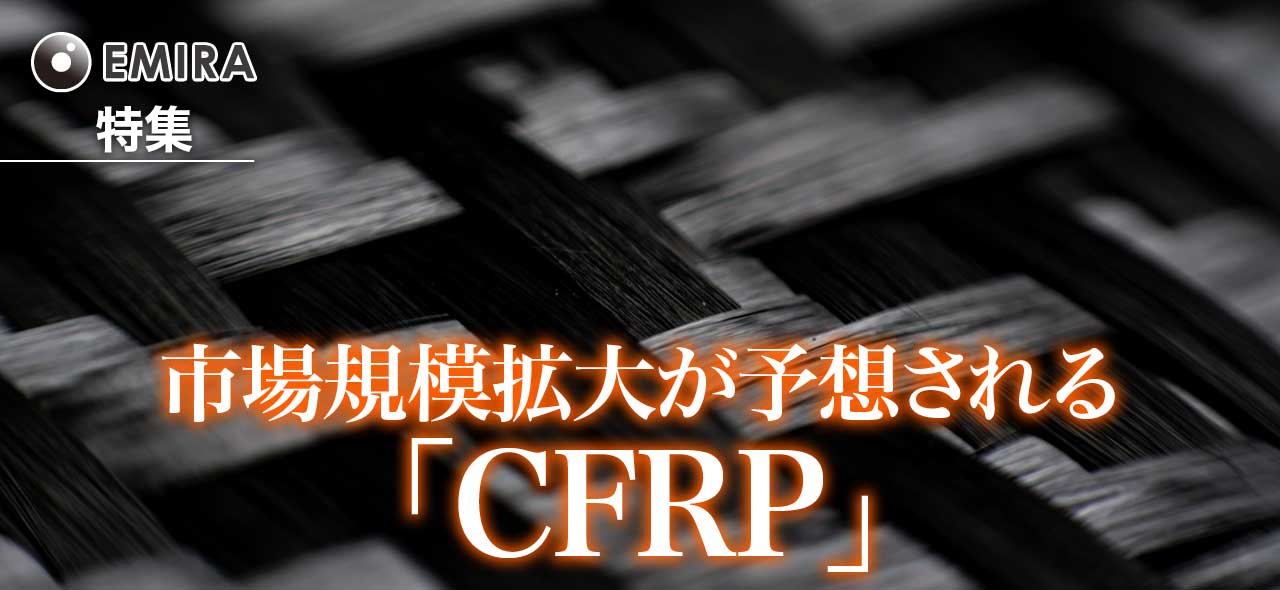
- 第1回炭素繊維とは? 新素材CFRPの将来性と今後の課題
- 第2回
- 第3回
- 「市場規模拡大が予想される「CFRP」」に戻る
-
この記事が気に入ったら
いいね!しよう -
Twitterでフォローしよう
Follow @emira_edit
- TOP
- 特集
- 市場規模拡大が予想される「CFRP」
- 炭素繊維とは? 新素材CFRPの将来性と今後の課題